Yhä useampi nuori Suomessa kokee yksinäisyyttä, ulkopuolisuutta ja eristäytyneisyyttä. Tähän ongelmaan pyritään puuttumaan NOPPA-hankkeella, jossa osallisuutta lisätään pelillistämisen avulla. …
Tekijät | Authors
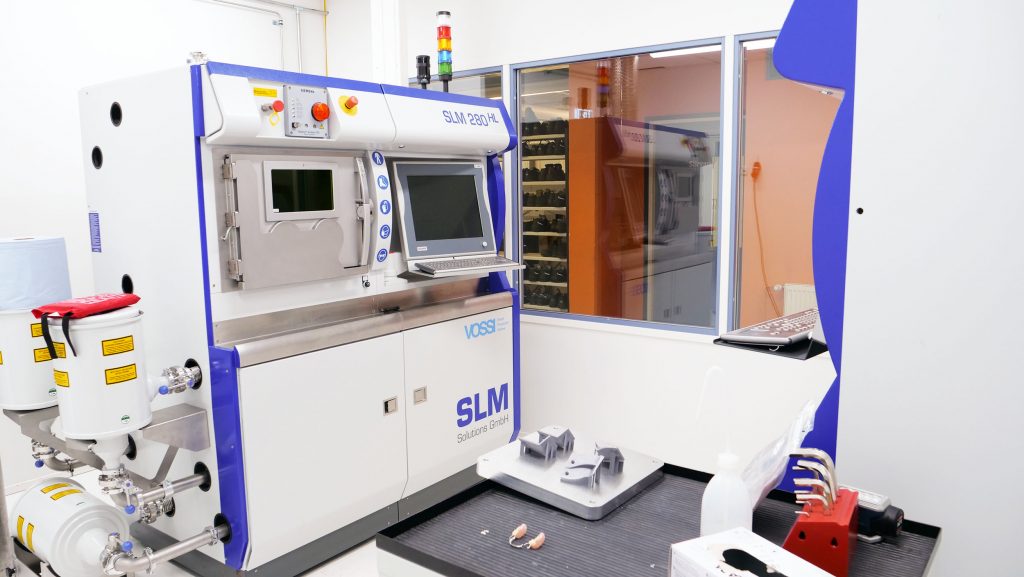
Metallien AM-tulostus tuottavaksi kappaleiden suunnittelu- ja jälkikäsittelyosaamisella
Metallien AM-tulostuksesta (additive manufacturing) kerrotaan menetelmänä, joka tarjoaa suunnittelijoille lähes vapaat kädet toteuttaa erilaisia kappaleiden muotoja ja rakenteita. Myös kappaleiden valmistuksen ajatellaan tapahtuvan täysin automaattisesti ja erittäin mittatarkasti. AM-tulostus tarjoaa kiistämättä uusia mahdollisuuksia niin suunnittelussa kuin valmistuksessa, mutta sillä on myös haastavia rajoitteita, joiden välttäminen edellyttää uutta tietämystä kappaleiden tulostusteknisestä sijoittelusta ja jälkikäsittelystä. Myöskään kappaleiden mittatarkkuus ei ole itsestäänselvyys.
Jauhepetitulostus
Materiaalien ominaisuuksista riippuen, lisäävässä valmistuksessa käytetään erilaisia prosesseja. Jauhepetitulostuksessa (Laser powder ped fusion, L-PBF) alustalle tasaisesti levitetty metallijauhe sulatetaan fuusiossa, joka saadaan aikaan lasersäteen avulla. Kuvassa 1 näkyy kuinka (a) lasersäde sulattaa metallijauhetta ja (b) lopputuloksena syntyvä kerroksittain rakentunut kappale.
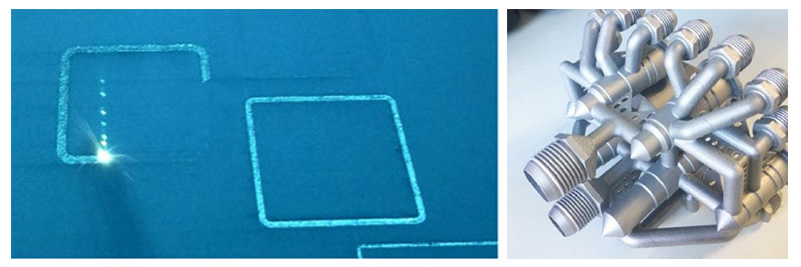
Kuva 1. Metallin (a) jauhepetitulostus (L-PBF) käynnissä ja (b) eräs valmis jauhepetitulostettu kappale. (Buchanan et al. 2017 p.10; Diegel et al. 2020 p.2-3.)
Kappaleiden jälkikäsittely
Kappaleita ei voi tulostaa ilmaan, vaan metallijauhe tarvitsee alustan, jolle se lasersäteen avulla sulatetaan, tyypillisesti alla olevaan edelliseen tulostuskerrokseen. Metallien L-PBF tulostuksessa kappale saattaa tarvita tukirakenteita esimerkiksi silloin kun kappaleen muoto on sellainen, että sen seinämä ylittää tukipinnan. Tukimateriaalia käytetään myös mm. kappaleen ankkuroimiseksi alustaan, vääntymisen estämiseksi, jäännösjännitysten vähentämiseksi ja lämmön pois johtamiseksi.
Tukirakenteista on siis hyötyä kappaleiden valmistusvaiheessa, mutta ne on myös poistettava kappaleesta ennen sen varsinaista käyttöä. Tämä ei useinkaan ole aivan helppo tehtävä, koska tukimateriaali on samaa metallia kuin itse kappalekin ja siksi usein lujaa ja vaikeasti työstettävää. Lisäksi tukimateriaalien poistaminen vie aikaa ja aiheuttaa lisäkustannuksia. Tukimateriaalien jälkityöstön tarvetta voidaan minimoida hyvällä suunnittelulla, kappaleen orientaatiolla tulostusalustalla sekä parhaassa tapauksessa käyttämällä kappaleen rakenteita myös tukirakenteina.
Tulostuskappaleiden jälkityöstö edellyttää niiden kiinnittämistä työstökoneeseen. Kappaleiden kiinnittämien sopivilla puristimilla työstökoneeseen on vakiintunut menetelmä teollisuudessa, mutta monimuotoisten metallisten L-PBF kappaleiden kiinnittäminen on tehtävä huolella, jotta ne eivät vaurioidu. Vaurio voi tapahtua, mikäli työkappale ei kestä puristusvoimia. Tällöin seurauksena voi olla taipuma, purse (jäyste) tai koko kappaleen rikkoutuminen. Kiinnikkeiden on asemoitava työkappale tarkasti ja lujasti, jotta vältetään kappaleen liikkeet ja tärinä koneistuksen aikana.
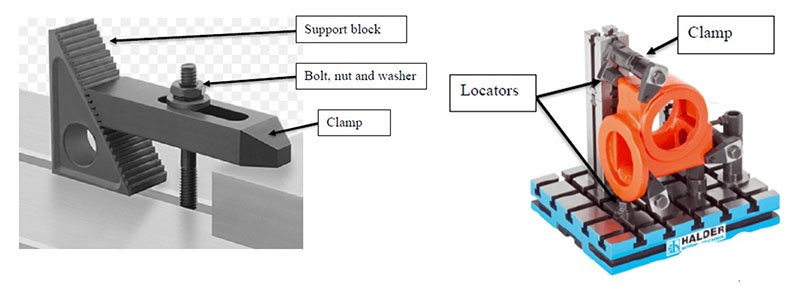
Kuva 2. Vakiokiinnitin ja modulaarinen kiinnitysjärjestelmä. (Modified from www.mcmaster.com; Halder 2021)
Kiristysjärjestelmä koostuu puristimesta, tukikappaleesta ja mutterilla varustetusta kiristyspultista (Kuva 2). Tällaisten puristimien avulla työkappale voidaan kiinnittää tukevasti työstämistä varten. Vakiokiinnittimet ovat erittäin monipuolisia työkaluja, mutta niitä käytettäessä työkappaleen pinnan on oltava tasainen ja suorakaiteen muotoinen. Vakiokiinnittimet soveltuvat pientuotantoon. Mikäli tuotetta tarvitaan enemmän kuin kymmenen kappaletta kannattaa harkita modulaarista kiinnitysjärjestelmää. Sillä saavutetaan parempi tarkkuus ja nopeampi käyttö verrattuna vakiokiinnittimiin.
Tukirakenteiden ja kappaleiden orientaation vaikutus jälkikäsittelytarpeeseen
On kiinnostavaa tietää kuinka kappaleiden ja valmistuksen suunnittelulla voidaan löytää uusia keinoja yksinkertaistaa ja tehostaa metallisten L-PBF kappaleiden jälkikäsittelyä. Tällöin on selvitettävä kuinka osien sijoittelu, suuntaus ja niiden tukirakenteet vaikuttavat jälkityöstötarpeeseen. Kuvassa 3 on esitetty tätä tutkimusta varten suunnitellut testikappaleet. Myös käytettävät työstömenetelmät, niiden parametrit ja edellä kuvatut kiinnitysmenetelmät vaikuttavat ratkaisevasti metallien AM-tulostuksen tuottavuuteen.
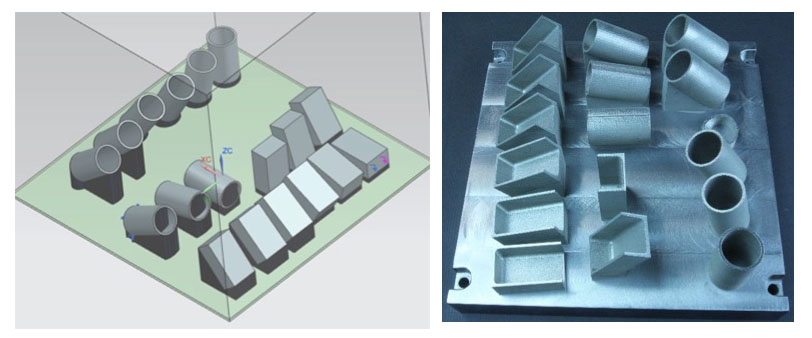
Kuva 3. Testikappaleet eri tulostuskulmissa 3D-mallina ja valmiina tulosteina.
Kappaleen tulostuskulma eli asento alustalla vaikuttaa laajasti koko valmistusketjuun. Se vaikuttaa AM-kappaleen valmistusaikaan, materiaalin tarpeeseen, rakennusalustasta irtoamiseen, tuen poistoaikaan ja pinnan laatuun. Jos tulostuskulmaan vaikuttava suunnittelu tehdään huolimattomasti, valmistuksen kokonaiskustannukset voivat nousta huomattavasti.
Putkimaisen kappaleiden rakennekulmien tulee olla alle 30° pystysuunnasta mitattuna, jälkikäsittelytarpeen minimoimiseksi. Yli 30°:n rakennekulmissa lisätukirakenteen tarve ja vääntymisriski kasvavat huomattavasti. Suorakaiteen muotoisille kappaleille tarvitaan tukirakenteita vain kahdelle alaspäin suuntautuvalle pinnalle, 40° ja 45° rakennekulmissa, kun taas putkikappaleet tarvitsivat tukirakenteita 45°-90° rakennekulmissa. Tämä tarkoittaa, että putket tulisi valmistaa pystysuorassa aina kuin mahdollista, mutta suorakaiteen muotoisille kappaleille on enemmän vaihtoehtoja. Yleensä on suositeltavaa valmistaa työkappaleet sellaisessa asennossa, jossa pienin pinta-ala on rakennustason suuntaan.
Tukirakenteiden poistaminen
Mitä enemmän tukirakenteita on, sitä enemmän työkappaleiden poistaminen alustalta vie aikaa. Saha on suositeltava menetelmä työkappaleiden poistamiseen rakennustasolta. Mikäli geometria estää sahauksen, niin joudutaan käyttämään vasaraa ja talttaa tai hydraulista leikkuria. Tukirakenteiden poisto kappaleista voidaan tehdä 3- tai 5- akselisella työstökeskuksella. 5-akselinen työstökone soveltuu hyvin kappaleiden jälkikäsittelyyn, koska sillä on mahdollista työstää monimutkaisempia muotoja kuin 3-akselisella koneella.
Suorakaiteen muotoinen työkappale voidaan kiinnittää suoraan koneistuspöydälle, mutta putkimaiset työkappaleet tarvitsevat erikoisleuat tukea ja kohdistusta varten. Sekä suorakaiteen muotoisia että putkimaisia työkappaleita on pyrittävä työstämään yhdellä kiinnityksellä. Tämä on hyödyllistä asetusajan, työstötarkkuuden ja koneistuskustannusten kannalta. Jos työstettävässä kappaleessa on monimutkaisia muotoja, kannattaa harkita erikoisjigejä (kappaleiden kiinnitysalustoja) kiinnitystä varten. Sylinterimäisten kappaleiden jälkityöstöön voidaan käyttää myös sorvia.
Luotettava kiinnitys voi kuitenkin olla vaikea toteuttaa kappaleen muodonmuutosriskin vuoksi tai siitä syystä, että kappaleeseen on AM-prosessissa syntynyt mittaepätarkkuutta. Kokeissa havaittiin 75° ja 90° rakennekulmissa tulostetuissa putkimaisissa kappaleissa ongelmallisia muodonmuutoksia. Ne olivat soikeita eivätkä sylinterimäisiä. Myös 90°:n rakennuskulmassa tulostettu kappale oli tynnyrin muotoinen. Suurin syy tähän ovat tukirakenteet. Mikäli niitä ei voidaan välttää, niin kasvattamalla kappaleen seinämän paksuutta, voidaan kappale myöhemmin työstää oikeaan mittaan, joka tosin johtaa pidempiin koneistusaikoihin ja materiaalin hukkaan.
Tukirakenteen poistaminen pyöreältä pinnalta on vaikeampaa kuin suoralta. Tähän vaikuttaa osan kiinnitys ja pyöreän pinnan asento. Sylinterimäiset kappaleet kannattaa kiinnittää pystyasentoon, jolloin työkalun pyöreä muoto kohtaa kappaleen pyöreän muodon, jolloin kappaleeseen saadaan myös sileä pinta. Suorat pinnat voidaan työstää helposti erilaisilla jyrsimillä. AM-kappaleiden jälkikoneistuksessa käytettävät koneistusparametrit vaikuttavat merkittävästi työkalujen kestoon. Vaikka tukirakenteet ovat onttoja, on ruostumattoman teräksen osalta silti käytettävä kohtuullisia työstöarvoja. Alhainen leikkausnopeus ja suuri lastunpaksuus yhdessä ovat huono valinta. Viimeistelykoneistuksessa tyypillisesti käytettävät työstöarvot sopivat myös tukirakenteiden koneistukseen. Tässä tutkimuksessa sovelletut työstöarvot on esitetty alla olevassa taulukossa.

Taulukko 1. Tutkimuksessa käytetyt työstöarvot.
Suunnitteluperiaatteita
Tehdyn tutkimuksen perusteella voidaan esittää seuraavat periaatteet, jotka kannattaa ottaa huomioon metallien AM-tulostuksessa ja sitä varten suunniteltavien kappaleiden muodoissa.
• Suorakaiteen muotoisissa kappaleissa tarvitaan tukirakenteita, jos rakennuskulma on yli 45°, vastaava kulma putkimaisilla kappaleilla on 30°.
• Suorakaiteen muotoisten kappaleiden tukirakenteiden tarve on suurin 40° ja 45° kulmissa.
• Sylinterimäiset työkappaleet tulee valmistaa pystysuunnassa ylimääräisten tukirakenteiden ja vääntymisen välttämiseksi, tai käyttää itsekantavia muotoja kuten timantti- tai pisaramuotoja.
Nämä periaatteet ovat ”nyrkkisääntöjä”, mutta vaatimukset tukirakenteille voivat vaihdella suuresti mm. riippuen kappaleen muista ominaisuuksista, kuten seinämänpaksuuksista. Kuvassa 4 on havainnollistettu (a) koekappaleiden rakennuskulmia ja kappaleiden (b) huokoista tukirakennetta.
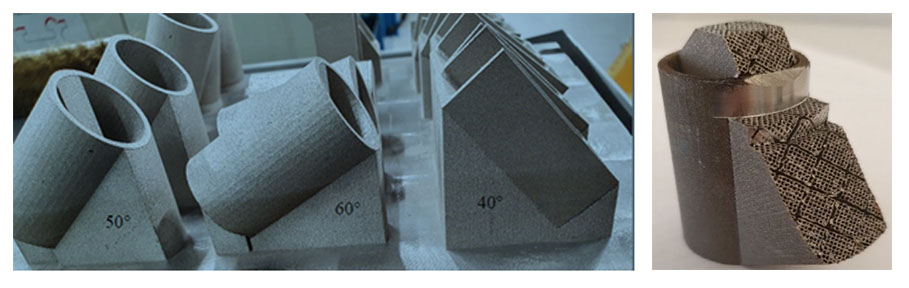
Kuva 4. (a) Koekappaleet tulostusalustalla eri rakennuskulmissa ja (b) kuva huokoisesta tukirakenteesta.
Metallien AM-valmistus antaa perinteisiä valmistusmenetelmiä enemmän vapauksia suunnitteluun, mutta tuo myös uusia haasteita ja rajoituksia. Suunnittelijan tulee ottaa huomioon tuotteen asennon vaikutukset, tuen tarve, kappaleen irrotus, tukirakenteiden poisto ja muut jälkikäsittelytarpeet. Suunnittelijan tulee myös tiedostaa, että huonosti valittu tulostuskulma voi aiheuttaa muodonmuutoksia tai vääristymiä kappaleeseen, huonon pinnan laadun ja aikaa vievän ja kalliin tukirakenteiden poistamisen.
Lähteet
Metsämäki, Kimmo 2021: Need of additional support structures and support removal in metal powered bed fusion. MSc-thesis, LUT-yliopisto https://urn.fi/URN:NBN:fi-fe2021120959806
Buchanan C., Matilainen V-P., Salminen A., Gardner L. 2017. Structural performance of
additive manufactured metallic material and cross-sections. Journal of Constructional Steel
Research Vol. 136. Pp. 35-48.
Diegel O., Schutte J., Ferreira A., Chan Y.L. 2020. Design for additive manufacturing
process for a lightweight hydraulic. Additive Manufacturing Vol. 36. Article 101446. Pp. 1-
9.
Tämä artikkeli perustuu Kimmo Metsämäen joulukuussa 2021 valmistuneeseen, LUT-yliopistoon tehtyyn diplomityöhön ”Need of additional support structures and support removal in metal powered bed fusion”, jota valvoivat Associate Professor (Tenure track) Ville Leminen ja M. Sc. (Tech.) Aditya Gopalunijonka. Työn toimeksiantajana ja ohjaajana toimi Turun ammattikorkeakoulusta D.Sc. (Tech.) Ari Putkonen.